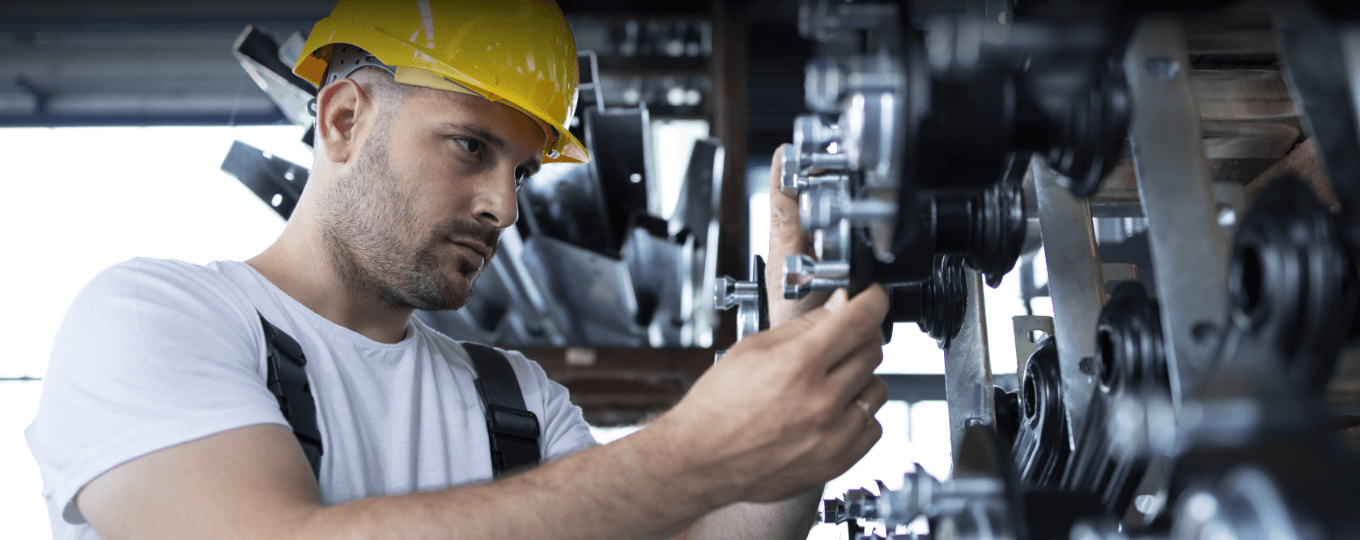
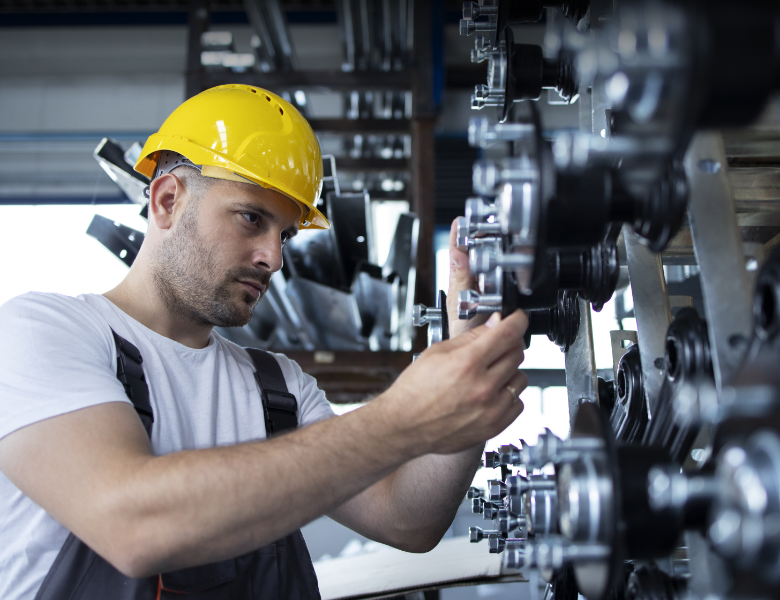
Remote Monitoring of Bearings
Mechanical failures from damaged bearings can lead to significant losses. To address this, InHand Networks provides the IG902 edge computing gateway. This solution collects real-time bearing data, processes it locally, and uploads it to the cloud for analysis and preventive maintenance, ensuring better monitoring and reduced downtime.
Background
Bearings are essential components in rotating machinery and are widely used across various industries. However, approximately 30% of mechanical failures worldwide result from bearing damage, severely affecting equipment performance.
During operation, factors like insufficient oil, collisions, and friction can raise bearing temperatures, leading to the “burning shaft” phenomenon. Fatigue wear, cracks, surface peeling, and impurities can cause abnormal vibrations and bearing damage. In extreme cases, anchor bolts may break, bearings may burn out, or bearing bushes may dislodge.
To prevent sudden failures, it is crucial to monitor the real-time condition of bearings and take preventive measures to ensure smooth operation.
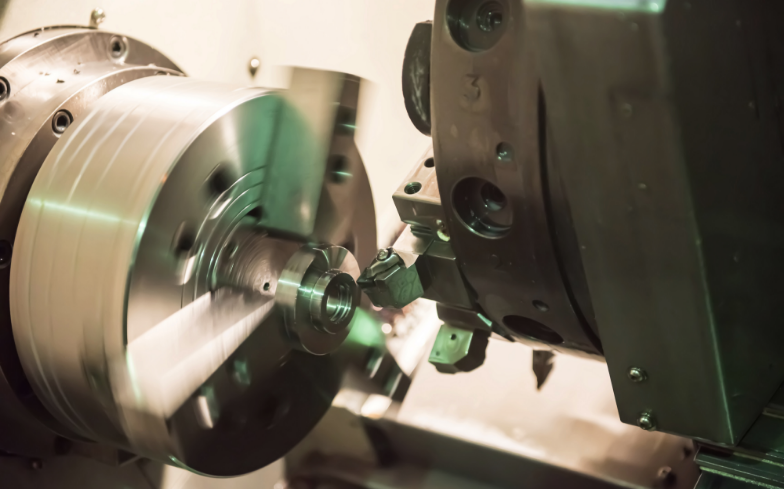
Customer Requirements
Real-time Health Monitoring
Continuously monitor the bearing’s status, including vibration, temperature, and load, to proactively identify potential problems and improve reliability.
Lifespan Prediction and Maintenance Planning
Predict bearing lifespan accurately and offer intelligent maintenance plans. This reduces maintenance costs and prevents unplanned downtime, keeping operations efficient.
Anomaly Alerts and Notifications
Establish a robust detection mechanism to monitor the bearing’s condition in real time. Send immediate alerts and notifications to operators when issues arise, helping to minimize potential losses.
Data Analysis and Performance Optimization
Provide advanced tools for analyzing data, optimizing bearing performance, and generating detailed reports for continuous improvement.
Solution
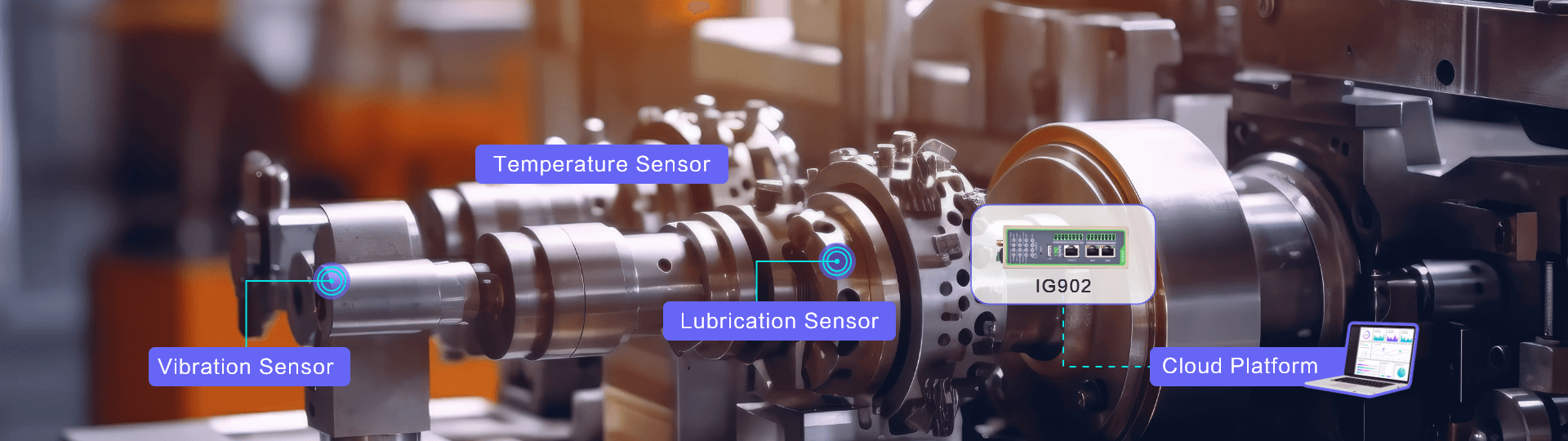
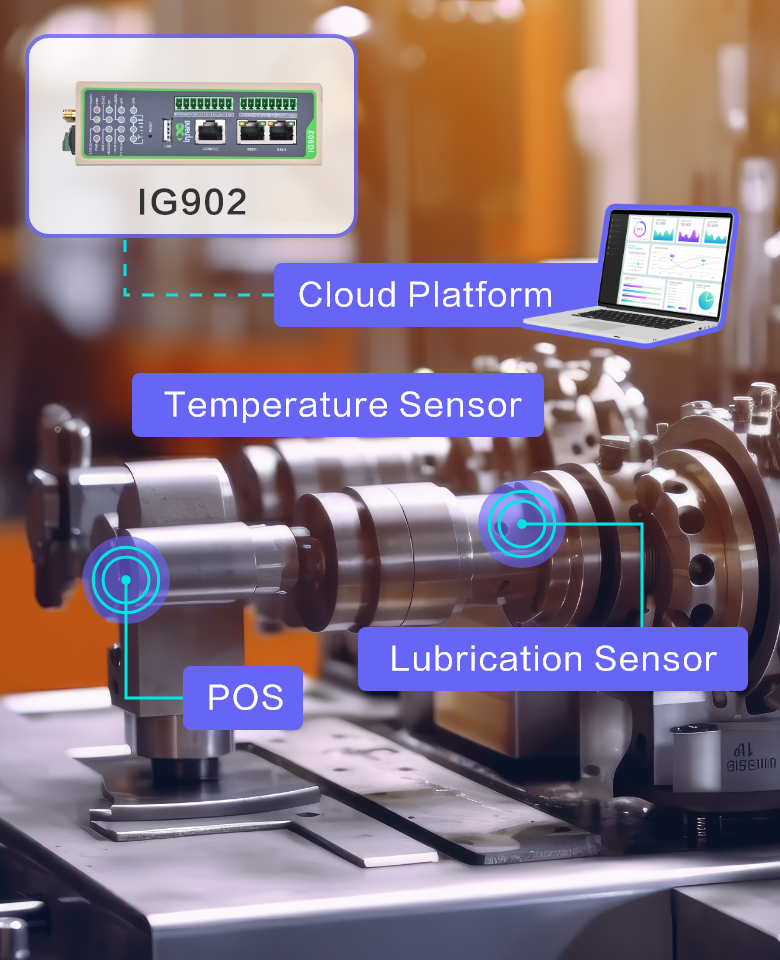
InHand Networks provides a remote monitoring solution for bearings powered by the IG902 industrial edge computing gateway. This solution collects key bearing data, such as vibration, lubrication, temperature, and abrasion, and uploads it to the cloud for analysis and predictive maintenance.
The system includes bearings, sensors (vibration, temperature, lubrication, etc.), the IG902, Device Manager, and a third-party cloud platform. Sensors transmit collected data to the IG902, where protocols are analyzed and converted into a standard format. The IG902 then sends this data to the cloud, where it is stored and analyzed.
In the cloud, advanced tools evaluate the bearing’s status and generate actionable insights for maintenance teams. This process ensures timely preventive maintenance, minimizes downtime, and extends the lifespan of bearings.
Benefits
Fast and Reliable Connectivity
The IG902 edge gateway ensures uninterrupted network access with LTE CAT4/CAT1, Wi-Fi, and wired connections. Its link redundancy technologies and security measures keep devices securely and consistently connected.
Quick and Easy Data Acquisition
Supporting multiple PLC protocols and major IoT clouds, the IG902 gateway allows on-site devices to connect to the cloud with simple configuration in just minutes.
Powerful Edge Computing
Equipped with an ARM Cortex-A8 processor, the IG902 delivers robust edge computing and data analysis capabilities. It preprocesses data collected from PLCs, reducing cloud load and enabling faster responses to data sources.
Effortless Remote Maintenance
Paired with the InConnect remote access service, the IG902 allows engineers to maintain PLC data anytime, anywhere, simplifying maintenance and improving efficiency.